Build-It TN
Exercise
The SIGPack company is a worldwide leading manufacturer of packing machines. They are manufacturing machines and plants for packing food into bags or cardboards. Thus these machines are designed and manufactured in many cases for a very specific product (e. g. the three-sided Toblerone package). Furthermore the plants also must be designed to given geometric properties in manufacturing hall of the customer.
You play the role of the planning engineer who has to plan and to design a plant for filling and packing of coffee. This work has to be done in close collaboration with colleagues.
Beside the unchangeable constraints of the geometry of the manufacturing hall the customer has the following requirements:
- two different kinds of coffee must be filled and packed simultaneously.
- the capacity per hour for the filling of coffee has to be 8000 and 11000 packages respectively.
- a random sample control has to be carried out in order to guarantee a constant quality of the packing. Therefore random packages were taken out of the production line, placed on a table and inspected by a worker.
- faulty packages are brought back to the filling funnel and emptied manually. Hygiene and security of the worker are very important aspects in this case.
- Definition of the material flow.
- Accessibility: Finished packets will be transported with a fork lifter.
- Filling in the coffee in the filling funnels is also done with a fork lifter.
- The foil has to be loaded inside the hall because the food needs always needs the same climatic conditions.
- Minimum number of needed persons (during the night the number of persons is reduced).
- It should be possible to overview the whole plant by the workers (2 persons).
Within this practice the planning of the packing plant is done with the help of virtual reality. The practice is done in the following two parts in two afternoons:
- Preparation of the planning task
- Performing the planning task together with a "customer"
1. Preparation of the planning task
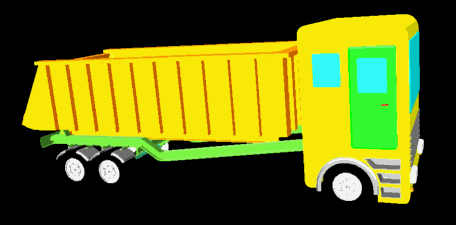
- Almost all parts of the machine and the plant are available in CAD. One missing part has to be designed at the CAD (UG), e.g. van, table, shelf.
- Exportation of the generated part into the VRML1 format.
- Visualization of the part on the large screen projection in the Visdome.
2. Carrying out the planning tasks
- Import of the generated parts into the Buildit system.
- Scaling of the generated parts.
- Performing the plant planning tasks with the parts of the modified object database.
- Evaluation within the team whether the planned plant suits the customer's needs.
For the planning task the following objects are available:
Conveyor belt with cups

The conveyor belt with cups will be used to place the open and empty coffee bags in a certain position under the filling unit for the coffee beans.
Unit for preparing the bags
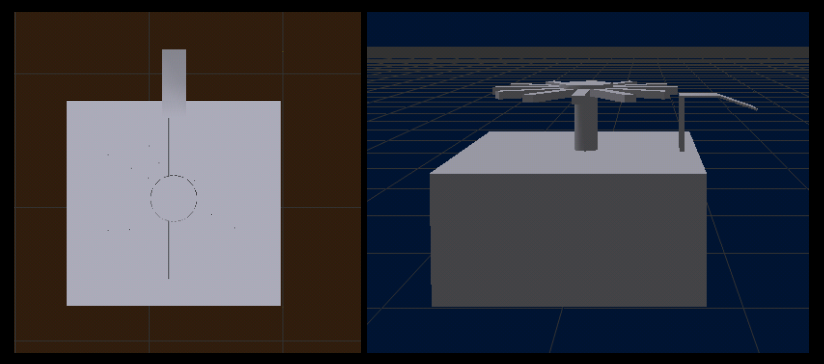
The bags are not ready to use but they have to be prepared first. After unwinding the foil tube it will be cut into suitable pieces and welded at one side so they can be filled with coffee.
Holder for the foil tube
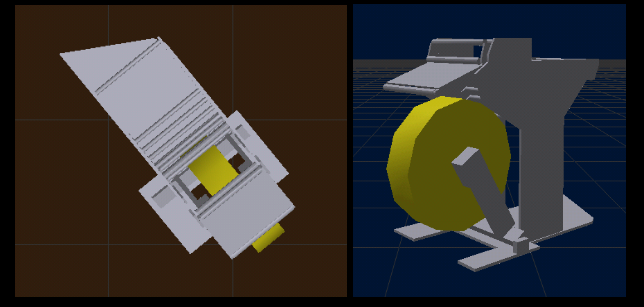
The coffee is packed in foils which protect the coffee against light and air. The foils are on a large roll which is placed in the holder. The device cuts the foil tube into suitable parts and melds them at one side so that a bag for the coffee results from that.
Foil roll
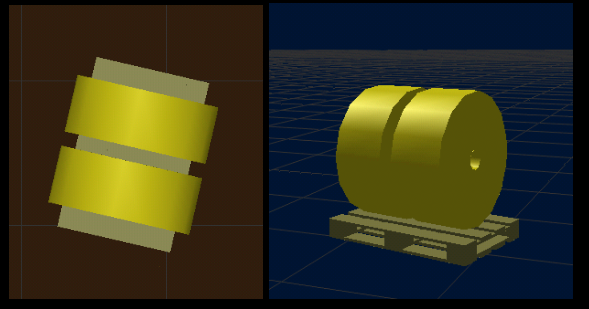
The foils are delivered on a palet and lifted into the foil holder by a fork lifter.
Funnel
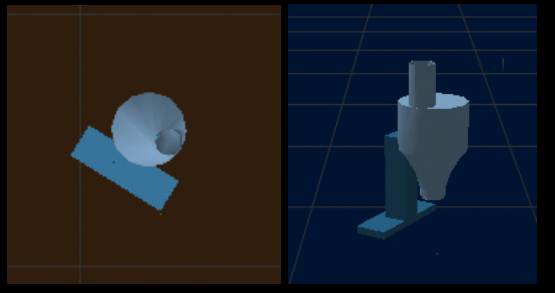
The funnel contains the coffee beans to be filled in into the bags. One funnel can fill up to 3'000 bags per hour. Tee funnel is also filled with a fork lifter.
Vacuum wheel
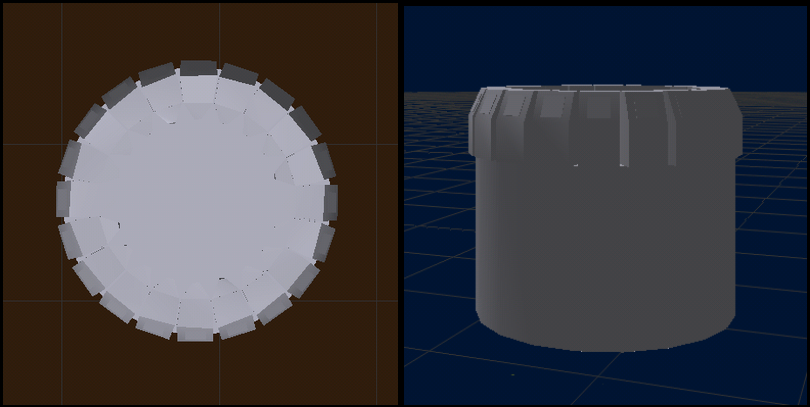
It is very important for the coffee that it is protected against influences from the environment in order to keep the flavor. After filling the bags with coffee they are vacuumized on the vacuum wheel. The wheel also has an additional welding unit to close the bags after the vacuumization process.
Conveyer belt
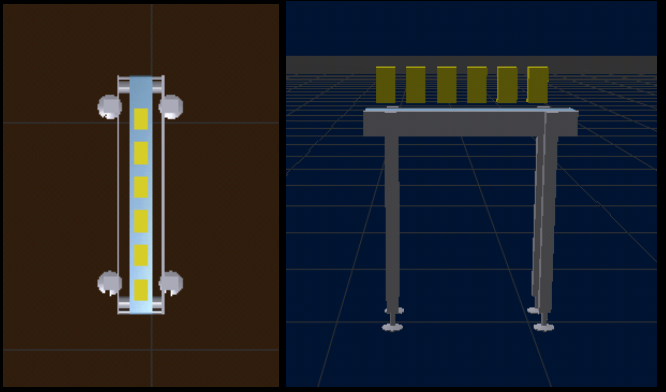
Once the bags are close they are put onto a conveyor belt to transport them to the next processing unit where the bags are put into cardboard boxes. The conveyor belt is also used by the workers to take random tests in order to proof if all processing steps for the filling and vacuumization are correct and without failures. Damaged bags are manually separated and placed on a table from which they put back into process at the right place.
Packing machine for cardboard boxes
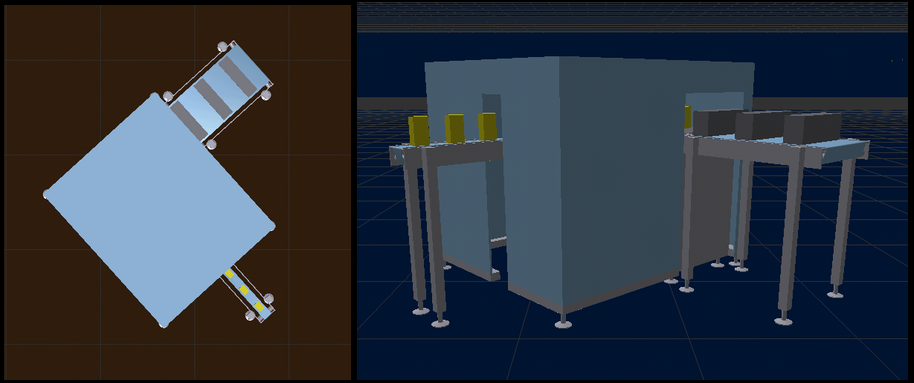
The bags which are filled and vacuumized are transported to a cardboard packing machine. Within this processing step 5 bags are packed into one cardboard package.
Holder for the cardboard roll
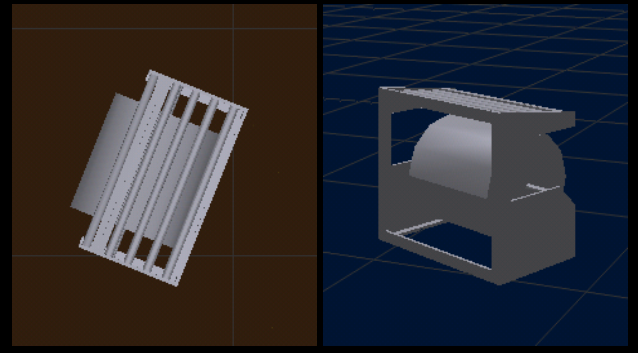
The large cardboard rolls are placed by a fork lifter into the roll holder. One cardboard roll lasts for approximately 5'000 packages. In order to guarantee a continuous workflow, two cardboard roll holders can be switched in series. The change of the cardboard rolls is done manually and the workers have to take care that the cardboard runs into the packing machine correctly.
Conveyor belt for the packages
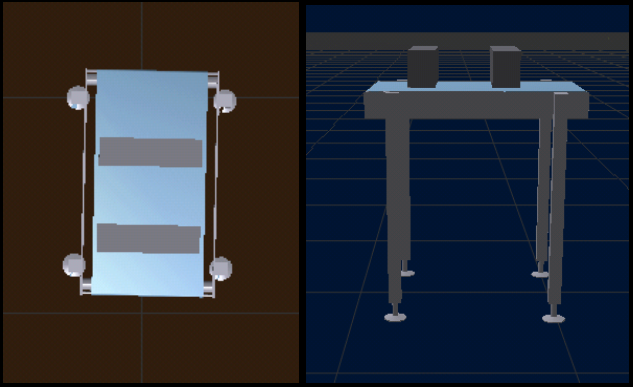
The filled packages have to be transported to a next processing unit where they are placed onto a palet. This unit is typically placed in a certain distance from the other machines since the machines for packing food and other machines have to separated from each other. Large conveyor belt are used to transport the boxes. In food industry typically conveyor belts are used for the transportation, outside the food processing roller conveyers are used.
Conveyer corner
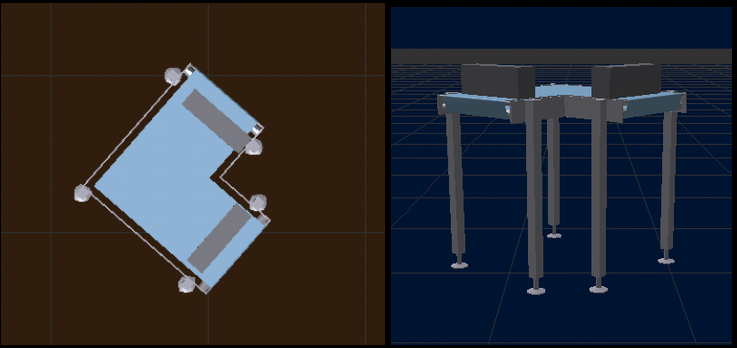
Since the whole packing plant has to fit into a given geometry of a building also conveyer corner are needed which change the transportation direction to 90°. The conveyer corner as well as the normal conveyer belt can be combined in any way.
Slide
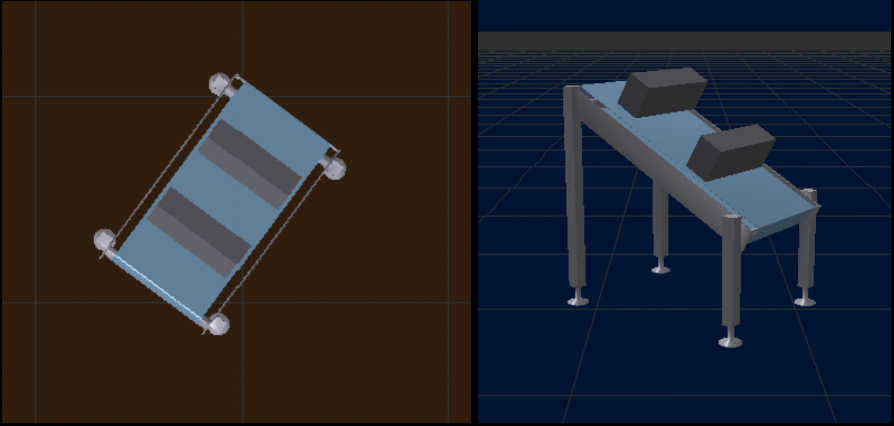
The packaging of the cardboard boxes is typically done on a different level. A slide is used to transport the boxes to this lower level. After the slide the boxes are not aligned anymore but this can be corrected with a specific roller conveyer before the boxes are placed on a palet.
Roller conveyer
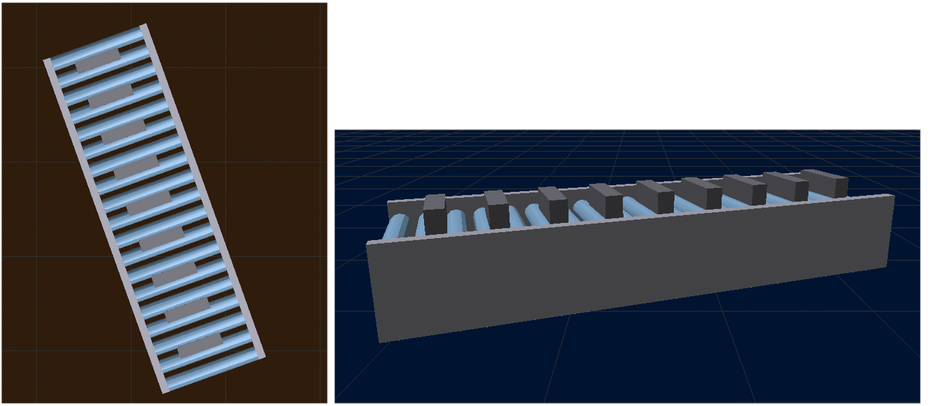
Outside of the area where food is handled typically roller conveyers are used since they have a lower susceptibility to trouble than normal conveyer belts. However, they do not fulfill the hygienic requirements for the food industry. Thus care has to be taken that the whole plant is separated into two section for the filling and packing of food and for the packing of the palets.
Packing machine for palets
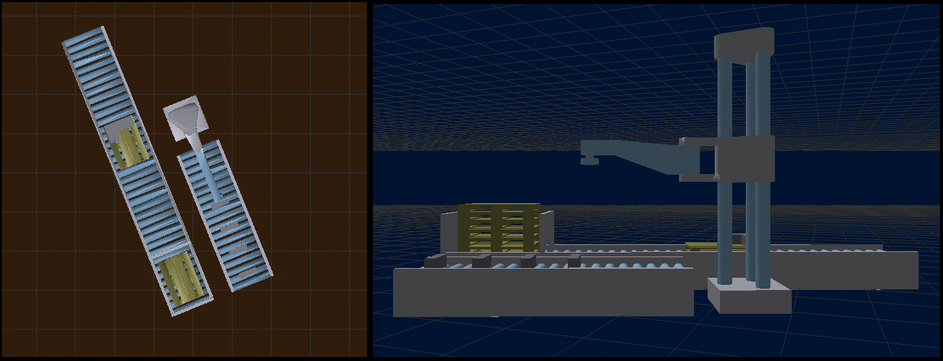
Behind the slide the packages come to a specific roller conveyer where every roll is driven separately. This allows to align the packages and to place them in equidistant order.
Palets are transported on a roller conveyer which runs parallel to the conveyer for the packages. The palets are taken from a storage room which has to be filled up by a fork lifter. The placement of the packages onto the palets is done by a robot as well the packaging of the palet itself (not in the picture).
Fork lifter
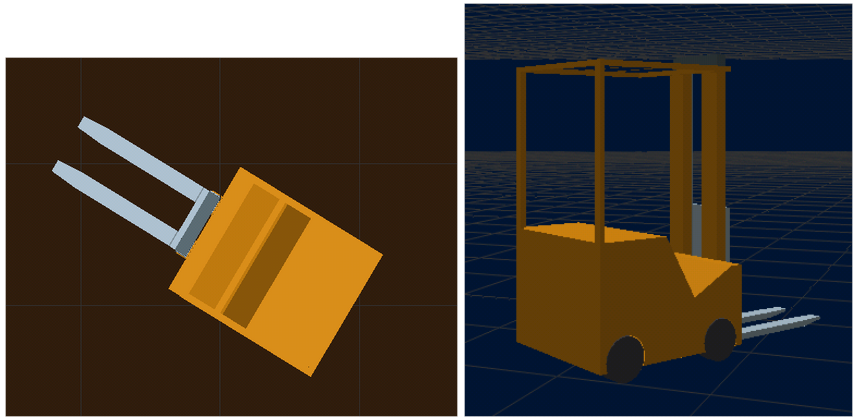
The model of the fork lifter is used to proof the accessibility to the position mentioned above. The scale of the fork lifter fits to other modules of the plant.
Palet
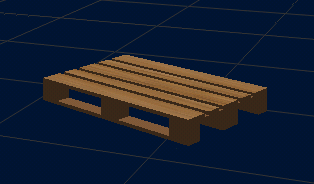
For placing the packages onto the palets they always have to be available. The palets are transported by the fork lifter from the storage room to the buffer where they can be taken by the robot.
Martin
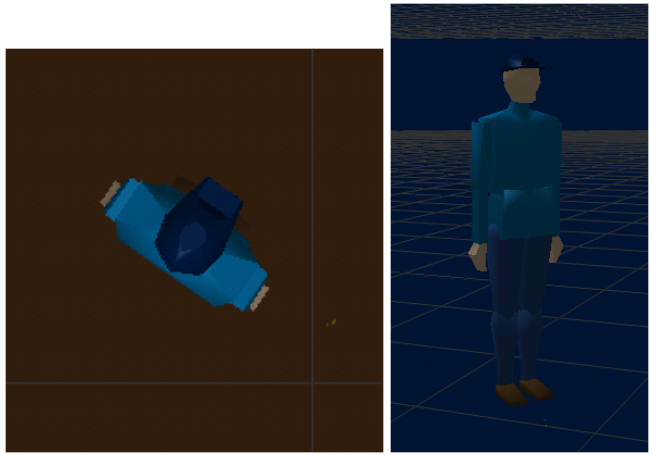
Martin is a typical workman and is used to proof the accessibility of the different machines of the plant. Together with an additional camera also Martin's field of view can be visualized.
Additional elements
Beside the modules of the plant described above additional elements are available for the handling of the Buildit system:
Camera
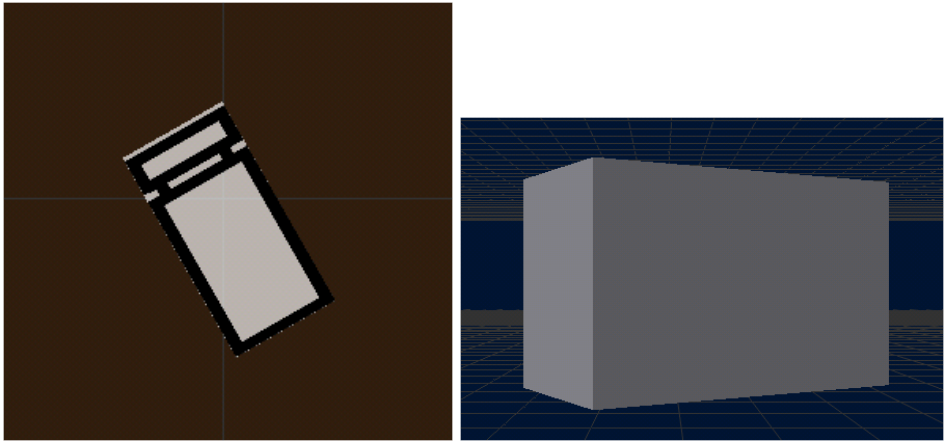
It is possible to navigate with camera on the two-dimensional view on the table. The view of the camera is visualized in the vertical three-dimensional view on the second screen.
Eyecatcher
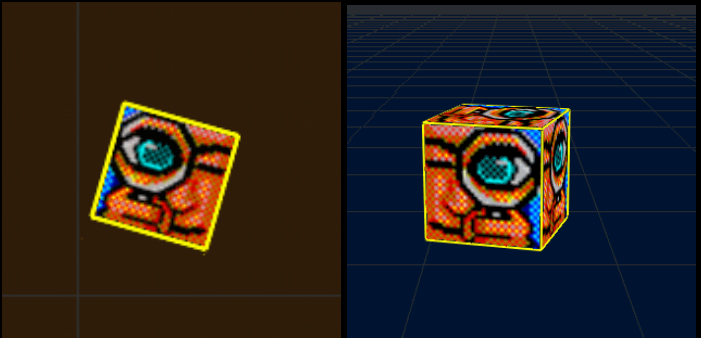
The eyecatcher is an object which is always followed by the selected camera. Thus the eyecatcher is another tool to manipulate the camera's direction of view. Furthermore it is possible to change the focus of the camera by using two eyecatchers. Thus it is possible to change to change from a fisheye view to a telescope.